ISO 13485 vs. ISO 9001
The Benefits of Voluntary ISO 13485 Compliance
Misunderstandings about International Organization for Standardization (ISO) management standard 13485, and how it compares to other industry standards such as ISO 9001 or Current Good Manufacturing Practice (cGMP), are common. Here, Narayan Krishnaswami, Senior Global Marketing Manager in the Applied Markets Business Unit at Sigma-Aldrich, offers a quick look at industry standards and explains what makes ISO 13485 unique, and how voluntary compliance differentiates Sigma-Aldrich.
A Brief Overview
Careful adherence to quality control standards throughout all stages of the manufacturing process is essential for patient safety. In 1938, the United States passed the Food, Drug and Cosmetic Act, created in an effort to protect the public from dangerous products. These cGMPs are revised regularly, and the production and testing procedures are designed to ensure high-quality products.
ISO 9001, first issued in 1987, and revised several times since then, is unlike cGMP. It focuses on business management standards rather than the product itself. By addressing the common problems businesses face at their source, and continuously seeking improvement, it allows product quality assurance.
Almost a decade later, in 1996, ISO 13485 was published. Using ISO 9001 as a model, the voluntary standard incorporates medical device regulations from around the world, and applies to the components and products included in a finished medical device. It has been updated several times (most recently in 2003) since being published, but certification requirements remain the same. For a company to qualify for ISO 13485, it must show that quality systems are properly implemented and maintained. A third-party assessor confirms whether standards are met, and issues a certificate.
Comparing ISO 9001 and ISO 13485
While ISO 13485 is based on ISO 9001, there are some key differences and additional requirements, in addition to product-specific demands and more stringent documentation requirements.
ISO 13485 calls for risk management to be in place for all stages of product realization, training and supervision of staff, project site specs, and prevention of contamination. Clinical evaluation must be carried out as part of design and development evaluation in line with regulatory requirements. The cleanliness of products and contamination control must be considered, as must the status of the product with respect to monitoring and measurement.
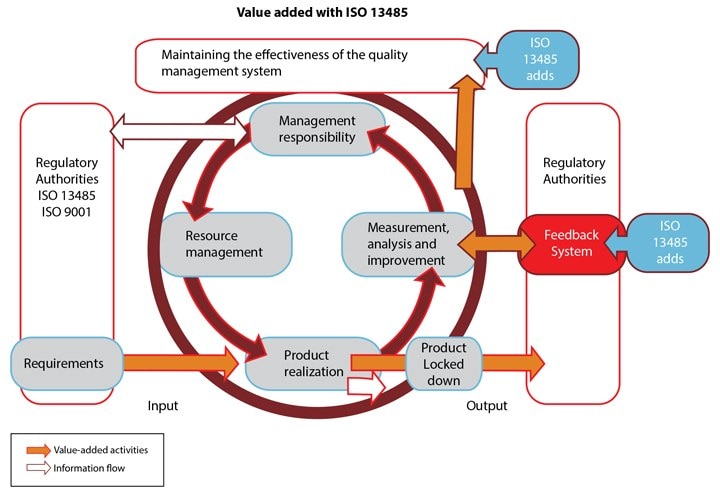
Key additional requirements of ISO 13485
- Risk management required at all stages of product realization
- Training and supervision of staff
- Contamination prevention
- Multiple documentation requirements
- Monitoring whether customer requirements are met, rather than more subjective customer satisfaction measures
- Maintaining the continued suitability and effectiveness of the quality management system, rather than striving for continuous improvement
Stricter Industry Standards
Manufacturers of in vitro diagnostics are increasingly calling on suppliers to assist them in meeting growing demands of industry regulators in both the US and Europe. Leading into 2014, stricter standards are expected across the board and regulators are also requiring details about design history that explains why particular chemicals are used and details about purity criteria.
For example, according to the US FDA, a pacemaker needs to be appropriately designed for its application, and every component that is used in it must be manufactured to the highest standards. Importantly, the regulations also apply to in vitro diagnostics, including the chemical and biological components they contain, so that any raw materials destined for a diagnostic or to be used in the manufacture of a diagnostic kit must meet specific requirements. Although the FDA does not explicitly call for compliance with ISO 13845, it is clear from 21 CFR part 820 of cGMP regulations that compliance with the ISO 13485 standard is valuable.
Manufacturers as well as regulators are looking for supply chain transparency to ensure that diagnostic manufacturers know about any changes to an ingredient’s manufacturing process, and any risks these may introduce. Changing, for example, the raw materials supplier, a synthetic route or the purification techniques used could impact the performance of the diagnostic test; studies to confirm accuracy would then have to be conducted and validated. Therefore, many test manufacturers demand continuity of supply, even if a newer, purer alternative becomes available, to avoid having to undergo further regulatory measures.
ISO 13485 Compliance
While ISO 13485 is not currently mandatory, and compliance is expensive, we believe that meeting the standards voluntarily is important. Customers in the in vitro diagnostics market increasingly want to know about procedures, so it is beneficial to gain ISO 13485 certification now rather than waiting for it to become compulsory.
Seven of our sites in the U.S. and U.K. are now certified, and more are undergoing the certification process. In addition, two other sites received ISO13485 certifications in September 2013. The sites in Woodlands, TX and Haverhill, UK are dedicated for the production of custom oligos for use in the IVD reagent development.
ISO 13485 Certified Sites: |
---|
As manufacturers are focusing on innovative tests, and look to outsource more of their core business (especially as more stringent regulatory demands increase the cost of compliance), we believe offering ISO 13485 certified raw materials is an added benefit to these diagnostics manufacturers and, ultimately, the patients who rely on the tests they make.
To continue reading please sign in or create an account.
Don't Have An Account?