Polymer-based Materials for Printed Electronics: Enabling High Efficiency Solar Power and Lighting
Ritesh Tipnis, Darin Laird, Mathew Mathai
Plextronics, Inc. 2180 William Pitt Way Pittsburgh, PA 15238
Material Matters 2008, 3.4, 92.
Introduction
The soaring global demand for energy has created an urgent need for new energy sources that are both cost-competitive and eco-friendly. Renewable energy technology, such as solar power and energy efficient solid-state lighting (SSL), could help satisfy these pressing needs. Solar power, however, is not widely commercialized because the cost of today’s silicon-based technology often limits its use mainly to large, on-grid applications. Similarly, the complex and expensive processes required for current SSL technologies have inhibited wide-scale deployment.
Printed electronics (PE) holds the promise of enabling low-cost, scalable solutions to address the issues faced by today’s solar and SSL technologies. PE exploits the ability of organic materials to be solution processed onto large area substrates at a fraction of the manufacturing cost associated with conventional vapor deposition techniques. As such, low-cost applications in lighting, power and circuitry are expected to fuel the growth of the PE industry from the current $1 billion to a $300 billion market in the next 20 years.1 Plextronics, Inc. is helping seed this market by developing materials for applications in organic photovoltaic (OPV) devices and organic light emitting diodes (OLED), with eventual applications in solar power and SSL.
Organic Light Emitting Diodes
In 2001, the energy consumption for lighting in buildings within the US was 8.2 quads (1 quad = 1.055 × 1018 joules), representing 22% of the total energy consumed.2 It is forecasted that efficient lighting can reduce 3.5 quads of electricity consumption by 2025. This translates to 41 less 1000 MW power plants, resulting in tremendous economic and environmental benefits. Solid-state white lighting, driven by OLED technology, can help realize this vision with energy efficient products to replace fluorescent lighting sources for general illumination beginning in 2010. There also exists significant opportunity for implementation in diffuse lighting applications that require flexibility, color tunability and low energy consumption.
The display industry has already begun to employ OLED materials in applications such as cell phones, mp3 players, and, most recently, televisions.3 However, significant market penetration remains elusive because performance parameters, such as device efficiency, lifetime, and operating voltage, require further optimization. In addition, considerable capital investment is required to retrofit manufacturing lines, which today use a series of vacuum-deposition processes for each color. Utilizing a manufacturing process based on solution processing will enable significantly higher materials’ utilization and lower energy consumption, whilst being cost-effective. Also, the use of an effective, solution-processable Hole Injection Layer (HIL) in the device stack directly impacts the performance of the device. An HIL enables efficient hole injection between the electrode and the neighboring light emitting/transport layers by reducing the energy barriers between the electrode and the semiconducting layer.4 Improved hole injection implies the capability to modulate the charge balance within the device, which in turn improves device lifetime. In addition, the effective reduction of energy barriers at interfaces lowers the operating voltage for OLEDs and also results in superior luminescent performance.5 Besides these functions, the HIL also planarizes the anode surface to prevent shorts, and blocks electrons from flowing out of the emitting layer and into the anode without recombination.6 All of these factors contribute to improvements in OLED performance, leading up to a commercially viable technology.
Organic Photovoltaics
A typical US coal-power plant emits, per GWh, about 1000 tons of CO2, 8 tons of SO2, 3 tons of NOx, and 0.4 tons of particulates.7 This has led to legitimate environmental concerns, which renewable energy sources like solar power can mitigate. However, today’s solar technology does not provide a clear path to meet the soaring demand. At the same time, the current primary source of solar technology, silicon-based solar energy, has not proven to be cost-effective due to significant raw material costs as well as the high infrastructure cost. The levelized cost of power from today’s solar installations is as much as ten times that of grid-supplied power depending on size of installation and geographical location. Second generation PV devices based on thin films of amorphous silicon, cadmium telluride (CdTe) or copper indium gallium diselenide (CIGS) are relatively inexpensive compared to silicon, but have not yet achieved wide scale adoption because they are still not cost competitive with grid pricing.
Polymer based OPV cells offer the potential to play a significant role as a zero-emission source of energy during the actual power generation process. However wide-scale commercialization requires a pathway towards large-scale, economical manufacturing. While low costs of raw materials and less complex manufacturing represent a major advantage in comparison to the currently dominant silicon-based solar cells, gains in efficiency are necessary to enable commercialization of OPV. Polymer-fullerene p-n junction (PNJ) solar cells are a promising approach to achieve such performance gains.
Materials for Printed Electronics
Polymer Semiconductors
Plextronics’ Plexcore® technology platform is comprised of semiconducting polymers and solution-processable inks that are designed to maximize the efficiency, lifetime and stability of PE devices. Plexcore OS, in particular, is a p-type organic semiconductor based on regioregular poly 3-hexylthiophene, RR-P3HT (Figure 1), a semi-crystalline, semiconducting polymer with exceptional spectroscopic and electronic properties. The material is easily synthesized via a method developed Plextronics’ co-founder, Dr. Richard D. McCullough.8-11 Plexcore OS 2100 is a grade of P3HT specifically designed for OPV and demonstrates the following properties:
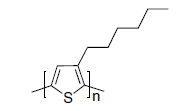
Figure 1.Poly 3-hexylthiophene (Prod. Nos. 698997, 698989)
- Electronics grade purity (<15 ppm metals) and high regioregularity enables high OPV performance through efficient light harvesting and hole transport.
- Readily formulated into printable inks with tailored material properties for a wide range of electronic applications.
- Consistent material supply via large-scale production provides minimized device and processing variability.
Data from recent batches of Plexcore OS 2100 demonstrate a production process that delivers consistent material properties batch-to-batch. Figures 2 and 3 provide batch-to-batch data for molecular weight (MW)/polydispersity index (PDI) and the metals content, respectively. Appropriate nanoscale morphology of thin films of RR-P3HT is required to achieve high charge carrier mobilities, a key factor in enabling efficient OPV device performance. Regioregularity, MW, and PDI are all known to influence this morphology, where, in general, high MW and low PDI deliver world-class performance. Maintaining these material properties in a controlled production process enables the end user to develop reproducible material processing and device fabrication. As such, variability is minimized to enable development focus in other areas such as device architecture.

Figure 2.Plexcore OS 2100 example batch data—molecular weight (left) and PDI (right).
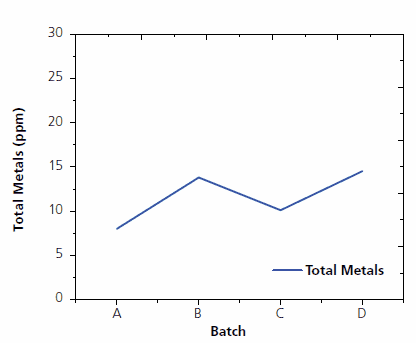
Figure 3.Plexcore OS 2100 example batch data—total metals
The metals content of organic materials has not been comprehensively studied to determine the impact on OPV performance. It is believed, however, that higher metals content may result in increased charge trapping within the thin film, which may lower charge carrier mobility, resulting in poor device performance. Within the OLED industry, metals content has been known to cause degradation and reduced device efficiency and lifetime. As such, Plextronics focuses on delivering materials with electronics-grade purity to minimize and eliminate potentially detrimental degradation mechanisms due to material purity. The combination of these properties leads to consistency in the performance of OPV devices fabricated with different batches of Plexcore OS 2100, as seen in Figure 4.
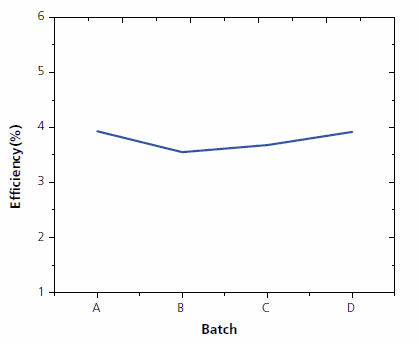
Figure 4.OPV efficency for P3HT:PCBM. Plexcore OS 2100 example batch data demonstrating OPV performance
The PNJ solar cell consists of an active layer that is a composite of a p-type (electron donating) light harvesting polymer and an n-type (electron accepting) semiconductor. Figure 5 shows the basic device architecture for an OPV cell comprising a photoactive layer. For the purposes of this discussion, the photoactive layer is based on a blend of Plexcore® OS 2100 (P3HT) and [6,6] phenyl C61 butyric acid methyl ester (PCBM), deposited on top of an organic hole transport layer (HTL), that planarizes the transparent anode, and also facilitates the collection of positive charge carriers (holes) from the light-harvesting layer. These photo-generated charges migrate to the collecting electrodes through this intimately mixed interpenetrating network. Examples of the best performing polymer organic cells have been based on the P3HT:PCBM junction.12-15 The system is characterized by phase-separation of the p- and n-components of the composite into discrete manifolds beneficial for charge transport and exciton dissociation. The I-V data in Figure 6 represents a single-junction OPV cell that was certified by the National Renewable Energy Laboratory (NREL) at 3.39% efficiency; a typical performance in a P3HT:PCBM system.
![OPV device stack. ITO: Indium Tin Oxide PCBM: [6,6] phenyl C61 butyric acid methyl ester Ca/Al: Calcium/Aluminium OPV device stack](/deepweb/assets/sigmaaldrich/marketing/global/images/technical-documents/articles/materials-science-and-engineering/organic-electronics/opv-device-stack.gif)
Figure 5.OPV device stack. ITO: Indium Tin Oxide PCBM: [6,6] phenyl C61 butyric acid methyl ester Ca/Al: Calcium/Aluminium
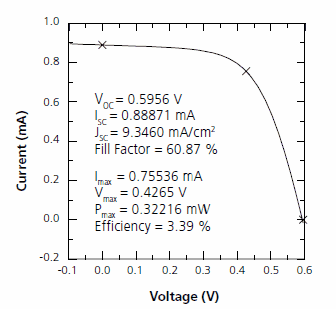
Figure 6.NREL certified I-V curve for Plexcore OS 2100:PCBM OPV cell. The device temperature is 27.0 ± 3.0 °C, the device area is 0.095 cm2 and the irradiance is 1000.0 W/m2.
Several material parameters directly impact short circuit current density (Jsc), open circuit voltage (Voc), fill factor (FF), and ultimately the efficiency (η) of an OPV device, as depicted in Table 1. Voc is a measure of cell potential and typically scales with the difference between lowest unoccupied molecular orbital (LUMO) level of the n-type semiconductor and the highest occupied molecular orbital (HOMO) level of the p-type semiconductor. Jsc is a measure of the maximum current density that could, in practice, be produced by a cell. It is principally influenced by the band-gap of the light-harvesting organic materials in an OPV device. Power In is typically defined as 1000 W/m2, which is equivalent to 1 sun (AM 1.5G). Conjugated polymers have strong, broad light absorption and most are semiconducting materials that exhibit a range of band gaps. FF is a figure of merit for how much power the cell can output versus the ideal power defined by the Jsc and Voc product. Many material properties, such as nanoscale morphology and charge carrier mobilities of the electrons and holes, affect the photophysical processes in an OPV cell. When optimized, this process leads to efficient charge separation and extraction; and FF is a composite parameter that includes contributions from all of these processes. Achieving > 7% cell efficiencies will require tailoring of all of these properties in combination. In addition, advancements in packaging, device architecture, and electrode engineering will contribute to the best performance of organic solar cells for commercial applications. Plextronics is actively pursuing development of higher efficiencies with the Plexcore PV platform. NREL-certified efficiencies in excess of 5% have already been achieved with improvements in materials and morphology.16
Polymer Conductors
Regioselective polymerization techniques used for synthesizing P3HT allow fine control of the absolute structure of the polymeric materials which support a variety of functionalities, thus enabling a greatly expanded platform for polymer design.17 For example, Plextronics has developed an inherently doped sulfonated solution of Poly(thiophene-3-[2-(2-methoxyethoxy) ethoxy]-2,5-diyl) (Figure 7). When combined with a matrix polymer and other additives in a solvent system, this ink formulation functions as an effective hole injection layer (HIL) for OLED devices18 and as a hole transport layer (HTL) for OPV devices. Plextronics provides 2% concentration solutions for application as an HIL - Plexcore OC 1100 and Plexcore® OC 1200 .
![Poly(thiophene-3-[2-(2-methoxyethoxy)ethoxy]-2,5-diyl), sulfonated Poly(thiophene-3-[2-(2-methoxyethoxy)ethoxy]-2,5-diyl), sulfonated](/deepweb/assets/sigmaaldrich/marketing/global/images/technical-documents/articles/materials-science-and-engineering/organic-electronics/polysulfonated.gif)
Figure 7.Poly(thiophene-3-[2-(2-methoxyethoxy)ethoxy]-2,5-diyl), sulfonated
Some of the performance benefits that Plexcore® OC offers as an HIL include:
- Reduced acidity, preventing anode degradation and ensuring improved device lifetime.
- Tunable properties such as work function, resistivity, surface energy, and viscosity, enabling researchers to optimize device performance.
- Compatible with multiple solvent systems and aqueous-based solutions, facilitating a variety of processing techniques.
The ability to solution process the HIL presents several advantages, including broad materials selection, flexibility in molecular design, lower materials consumption and processability at ambient temperature and atmospheric pressure. One of the unique features of Plexcore OC inks is the ability to be tuned to match the work function, resistivity, and viscosity, for example, required for specific device architectures and application techniques. This tunability provides the versatility needed to develop new solid state lighting (SSL) device stacks.
Figure 8 shows a typical Phosphorescent LED (PHOLED) device architecture where the HIL layer, such as Plexcore OC 1100 or 1200, is deposited onto the anode via spin coating. Figure 9 shows representative performance data for a green PHOLED made using Plexcore OC. The turn-on voltage of the device is at the band gap of the emitter, indicating low interfacial energy barriers, which could be attributed to efficient hole injection. This leads to efficiencies as high as 14-15 cd/A being obtained in a PHOLED device architecture, with modest efficiency loss as the current density is increased.
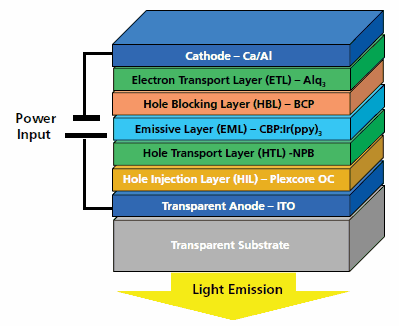
Figure 8.OLED device stack
ITO: Indium Tin Oxide
NPB: N,N’-Bis(naphthalen-1-yl)-N,N’-bis(phenyl)benzidine (Prod. No. 556696)
CBP: 4,4’-N,N’-dicarbazole-biphenyl (Prod. No. 699195)
Ir(ppy)3: tris-[2-phenylpyridinato-C2,N]iridium(III) (Prod. No. 694924)
BCP: 2,9-dimethyl-4,7-diphenyl-1,10-phenanthroline (bathocuproine)(Prod. No. 699152)
Alq3: tris-8-hydroxyquinoline aluminium (Prod. No. 697737)
Ca/Al: Calcium/Aluminium
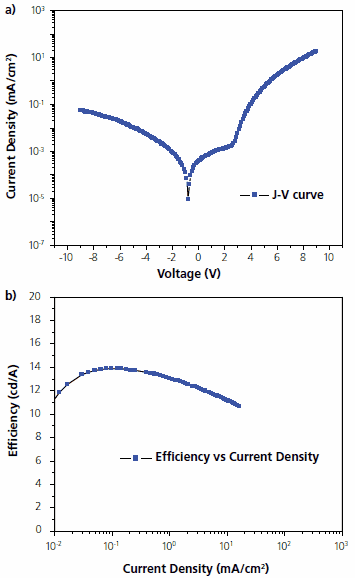
Figure 9.(a) J-V curve; (b) efficiency vs. current density for a green PHOLED with device architecture shown in Figure 8.
One of the critical aspects for a SSL luminaire is the ability to achieve high brightness at low operating voltage. Figure 10 shows the power efficiency of the device shown on the previous page as a function of operating brightness. The presence of the HIL reduces injection barriers leading to lower operating voltage and improved efficacy (Lumen/Watt) at higher brightness. Maintaining higher efficacy at higher brightness ensures more light output for lower cost. It is expected that SSL products enabled by Plexcore® OC will help realize the energy efficient lighting of the future.
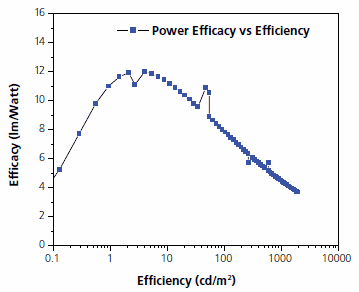
Figure 10.Power efficiency of a PHOLED utilizing Plexcore OC as the hole injection layer (HIL). As observed, the loss in power efficacy is minimized up to 1,000 units of brightness.
Conclusion
Printed Electronics could dictate the future of electronics and the energy industry by employing OPV and OLED devices in various applications, such as solar modules and luminaires based on solid state lighting. In addition, applications that integrate light and power may enable a new market segment for economical and environmentally friendly products. Plextronics’ polymer products such as Plexcore OS have the potential to yield high-efficiency OPV devices to serve the renewable energy market. Also, Plexcore OC ink systems that have already demonstrated exceptional performance in OLED devices, can enable SSL products and help meet the low energy consumption demands of the lighting market.
References
To continue reading please sign in or create an account.
Don't Have An Account?